Automation anxiety is largely misplaced
The experience of companies like Nucor is that we have little to fear from automation -- provided we stop treating people as semi-programmable robots, and instead give workers the incentives, discretion, skills, and safety to be creative in their jobs.
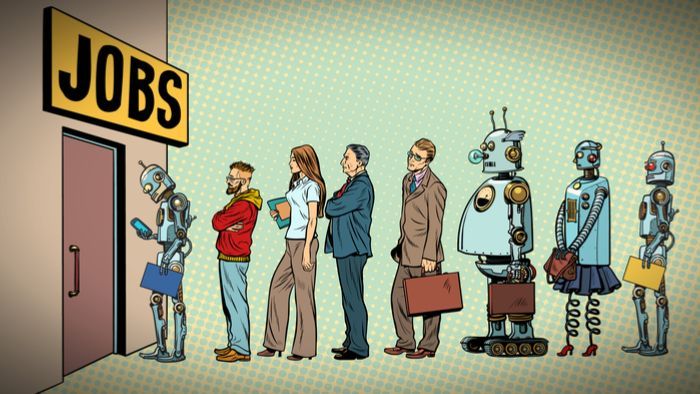
As long as we to stop treating people as semi-programmable robots.
Noah Smith, one of my favorite economics writers, has recently published an interesting post on the impact of automation on workers. In it, he makes a compelling argument that automation ultimately benefits employment:
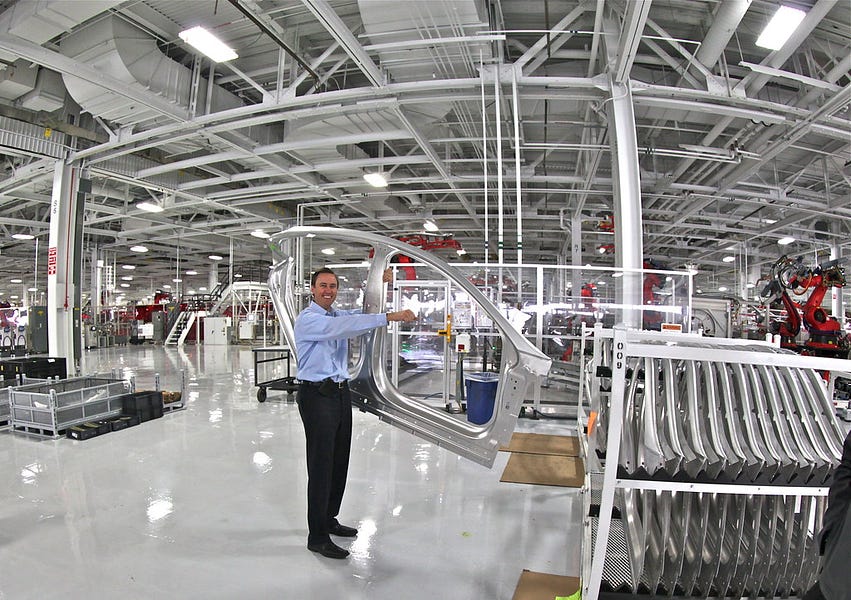
One anecdote that supports the wealth of research Smith cites in his piece is a company called Nucor, which I've come to know well as I conducted research for Humanocracy. Nucor is the largest steel maker in the United States, and arguably the process automation leader in the steel industry.
As Nucor embraces automation, it has also steadily expanded employment--a pretty remarkable feat in an industry that as a whole has lost jobs in the last few decades.
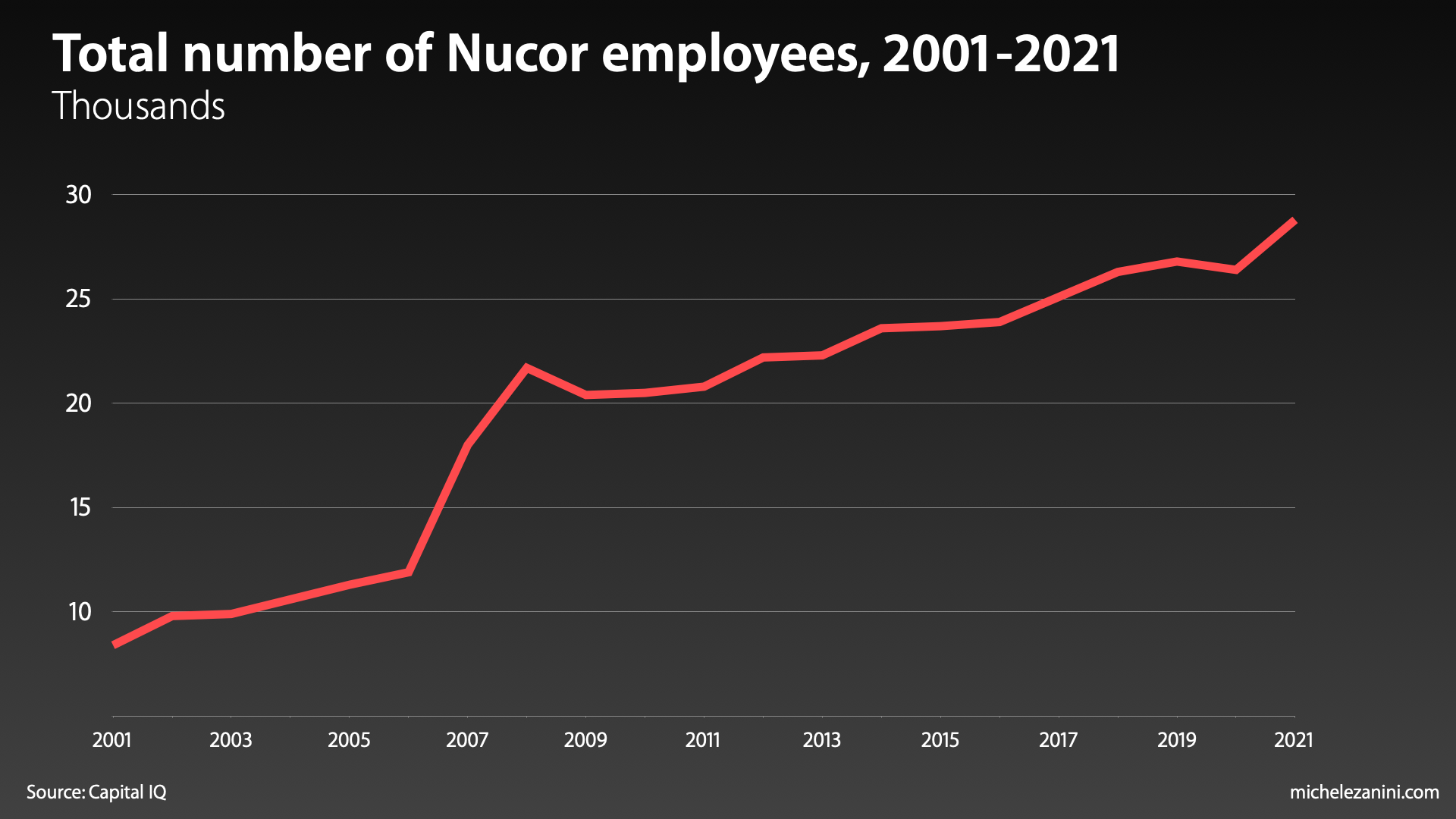
The interesting thing about Nucor is that a lot of automation is driven by frontline employees.
There are several reasons for this, starting with incentives. Nucor workers are paid weekly bonuses based on productivity. Base pay for production teams is about 75 percent of the industry average, but once a team’s output exceeds a threshold, typically 80 percent of the plant’s rated capacity, a bonus plan kicks in. The bonus threshold is fixed and gets adjusted only when major capital investments increase the rated output of a particular piece of machinery or the entire plant. Knowing this, team members have a powerful incentive to “sweat the assets,” since the only way to increase their bonus is to produce more steel for a given amount of capital. In practice, this means using their ingenuity to shrink costs and speed up workflows. When a new piece of equipment is installed, it’s not unusual for a team to blow through the rated capacity level in a matter of months.
Frontline teams also have the freedom to experiment with new production techniques, as well as the skills to do this autonomously. Not all the improvement opportunities the teams work on have to do with process automation, but many do (such as using remote sensors to replace the manual measurement of molten metal in the furnace cauldron). Innovation isn't just up to the white collars in engineering--it's everyone's job, every day.
At the same time, Nucor doesn't do layoffs, even during a downturn. The company’s long-standing promise to employees is, “Do your job well today, have it tomorrow.” This means that workers aren't afraid to suggest and try improvements--nobody’s worried about being replaced by a smart machine.
The experience of companies like Nucor is that we have little to fear from automation -- provided we stop treating people as semi-programmable robots, and instead give workers the incentives, discretion, skills, and safety to be creative in their jobs. That choice, of course, is ours.